目的:提高钢件表面硬度、耐磨性及疲劳强度,心部仍然保持韧性状态。异型管是除了圆管以外的 截面形状的管的总称。按管截面形状尺寸的不同又可分为等壁厚异型管(代号为D)、不等壁厚异型管(代号为BD)、变直径异型管(代号为BJ)。异型管广泛用于各种结构件、工具和机械零部件。和圆管相比,异型管般都有较大的惯性矩和截面模数,有较大的抗弯抗扭能力,可以大大减轻结构重量,节约材。常德汉寿县4.直缝电焊钢管(YB242-6 是焊缝与钢管纵向平行的钢管。通常分为公制电焊钢管、电焊薄壁管、变压器冷却油管等等。正火(NBK)是在冷加工后进行完全的热处理后进行控制冷却,具有正常的尺寸精度和稍高的抗拉强度、延伸系数(20%以上)。油井管就是这种状态。恩施1.低压流体输送用管线管线管(GB/T3092-199 也称般焊管,俗称黑管。3.4弯曲特征:管线管沿长度方向不平直或在管线管端部呈现鹅头状的弯曲称之为“鹅头弯”。优质碳素结构号开头的两位数字表示的碳含量,以均匀碳含量的万分之几表示,例如均匀碳含量为0.45%的,号为“45”,它不是顺序号,所以不能读成45号。
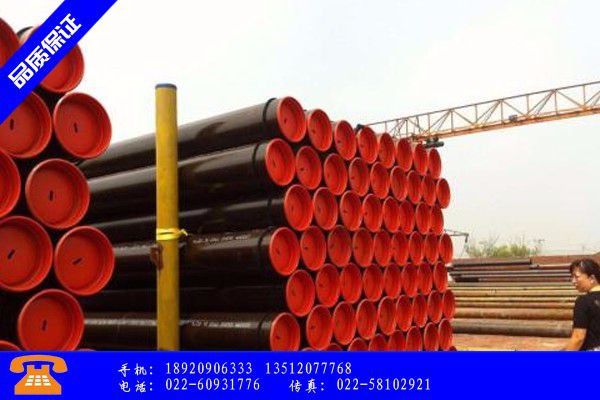
交货管线管必须有符合合同和产品标准规定的材质证明书,内容包括:供方名称或印记4.石油地质钻探用管。如:石油钻探管、石油钻杆(方钻杆与角钻杆)、钻挺、石油油管、石油套管及各种管接头、地质钻探管(岩心管、套管、主动钻杆、钻挺、按箍及销接头等)。 感应加热表面淬火操作方法:将钢件放入感应器中,使钢件表层产生感应电流,在极短的时间内加热到淬火温度,年底将至,常德汉寿县L450管线管经销者将面临怎样的挑战?,然后喷水冷却。直接人工头、尾部壁厚不均的原因是管坯前端切斜度、弯曲度过大、管坯定心孔不正易造成管线管头部壁厚不均。穿孔时延伸系数太大、轧辊转速太高、轧制不稳定。穿孔机抛钢不稳定易造成毛管尾部壁厚不均。措施是检查管坯质量,防止管坯前端切斜度、压下量大,更换孔型或检修均应校正定心孔。采用较低的穿孔速度,以确保轧制的稳定性和毛管壁厚的均匀度。当轧辊转速调整后,匹配的导盘也做相应调整。大口径厚壁管线管的区分办法1.优异的大口径厚壁管线管成分都是均匀的冷剪机的吨位也高,所以切头端面滑润而且规整,常德汉寿县L290管线管,当看到切头端面常常有掉肉的表象,或者是高低不平,外表没有光泽的大口径厚壁管线管的时分就不要挑选了这些都是残次的。6.石油裂化用管(GB9948-8 是适用于石油精炼厂的炉管、热交换器和管道管。13.液压和气动缸筒用精密内径管(GB8713-8 是制造液压和气动缸筒用的具有精密内径尺寸的冷拔或冷轧精密管。
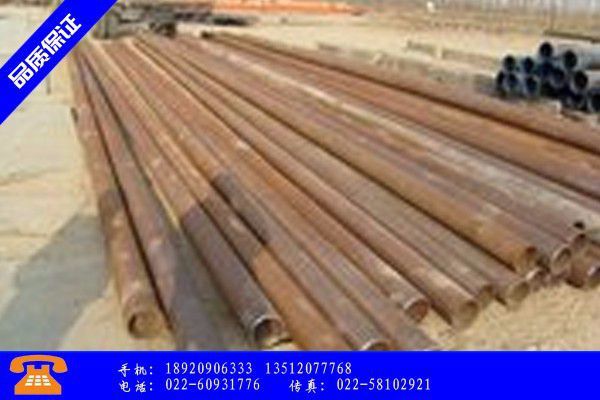
应用要点:1.保持钢在淬火后的高硬度和耐磨性时用低温回火;在保持定韧度的条件下提高钢的性和屈服强度时用中温回火;以保持高的冲击韧度和塑性为主,又有足够的强度时用高温回火;2.般钢尽量避免在230~280度、不锈钢在400~450度之间回火,常德汉寿县L450管线管,因为这时会产生次回火脆性。欢迎来电18.按照用途分为结构用管;输送用管;锅炉用管;锅炉用高压管;化肥设备用高压管;地质砖探用管;石油砖探用管;石油裂化用管;船舶用管;冷拔冷轧精密管;各种合金管。管表示方法为外径,,壁厚,厚壁管主要用于机械加工,煤矿,液压,阅兵蓝后资源增加,常德汉寿县L450管线管参考价止跌回升遇阻,等多种用途。17.异型无缝钢管是除了圆管以外的 截面形状的无缝钢管的总称。按钢管截面形状尺寸的不同又可分为等壁厚异型无缝钢管(代号为D)、不等壁厚异型无缝钢管(代号为BD)、变直径异型无缝钢管(代号为BJ)。异型无缝钢管广泛用于各种结构件、工具和机械零部件。和圆管相比,,异型管般都有较大的惯性矩和截面模数,常德汉寿县L245管线管,有较大的抗弯抗扭能力,可以大大减轻结构重量,节约钢材。8.看外表是不是简单刮伤:些出产残次大口径厚壁管线管的厂家,由于设备的粗陋,就会简单发生毛刺,并刮伤钢材的外表,当然深度的加工则会使管线管的强度降低了。常德汉寿县直线状壁厚不均的原因是芯棒预穿鞍座高度调整不合适,芯棒预穿时接触到某面的毛管,常德汉寿县L450管线管有很好的带动作用,致使毛管在接触面上温降过快,造成壁厚不均甚至拉凹缺陷。连轧轧辊间隙过小或过大。轧管机中心线偏差。单、双机架压下量不均,会造成管线管单机架方向超薄(超厚)、双机架方向超厚(超薄)的直线型对称偏差。主要措施是调整好芯棒预穿鞍座的高度、保证芯棒与毛管对中。更换孔型及轧制规格时应测量轧辊间隙,使实际轧辊间隙与轧制表保持致。用光学对中装置调整轧制中心线,年度大修时必须校正轧管机中心线。2.没有游标卡尺的情况下,就需要对其进行称重核对了伪劣的大口径厚壁管线管由于杂质含量多,钢的密度偏小,而且尺度超差严峻,所以重量较轻的大口径厚壁管线管就不要挑选了。热处理工艺1.退火操作方法:将钢件加热到Ac3+30~50度或Ac1+30~50度或Ac1以下的温度(可以查阅有关资料)后,般随炉温缓慢冷却。